Productivity, quality and flexibility are decisive for a competitive edge. But to achieve optimal results, it is no longer enough to deploy the best injection moulding equipment; it is all about leveraging its maximum potential. inject 4.0 – this is ENGEL's approach for meeting these challenges. At Fakuma 2015, the machine manufacturer is presenting products and solutions that are already available today to support production optimisation towards the goals of the "Industry 4.0" concept.

The ENGEL stand at Fakuma 2015 has been designed as a smart factory. The machines are networked with each other. Self-adapting, decentralised systems boost process capability and quality.
"Industry 4.0 is above all one thing: a tremendous opportunity that we want to take advantage of together with our customers," says Dr Stefan Engleder, CTO of ENGEL AUSTRIA, while at Fakuma 2015 in Friedrichshafen, Germany. "Industrial revolutions occur on average every 50 years. We view it as a great opportunity to experience one and be involved in shaping it for our industry." However, Dr Engleder emphasises that he does not consider the word "revolution" to be very appropriate. "The changes that we are currently experiencing are more like an evolution." Thus for ENGEL, Industry 4.0 is not a new idea, but is already long-established daily practice in many areas. What is new is the fact that, under the inject 4.0 brand, ENGEL is bundling the products and services that are already available now together with coming developments that help turn a manufacturing operation into a smart factory.
To achieve a "smart factory" is the goal of inject 4.0. With the help of the networking and integration of production systems, the systematic exploitation of process and production data and the use of adaptive production systems, the manufacturing processes in a smart factory continuously optimise themselves. "We're not talking about smart products," says Engleder. "That is the domain of the processor. We see it as our job to aid our customers in optimising their manufacturing processes."
The smart factory is based on three core elements:
- smart machines that boost process capability and quality with self-adapting, decentralised systems,
- smart production to ensure high levels of productivity thanks to horizontal and vertical data integration, and
- smart services that improve availability quickly and efficiently thanks to close proximity and the use of remote maintenance tools.
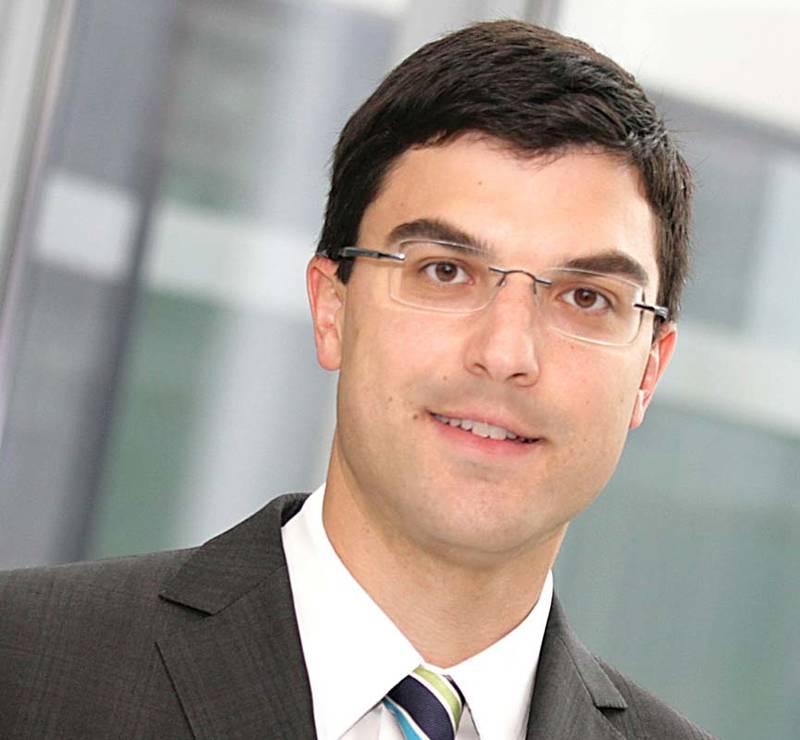
Dr. Stefan Engleder, CTO: "Industry 4.0 is above all one thing: a tremendous opportunity that we want to take advantage of together with our customers."
smart machines: distributed intelligence boosts process capability
The human-machine interface is becoming increasingly important. It should also be possible to set up, operate and above all monitor complex injection moulding processes easily and intuitively. In the smart factory, the system operator is supported by a variety of assistance systems to achieve this. They all have the goal of boosting process capability without requiring the operators to acquire special skills. Examples of such systems are the iQ weight control and the iQ clamp control software solutions and the ENGEL e-flomo temperature-control water distribution system. The iQ products continuously analyse process parameters relevant for productivity and quality, recognise deviations from the target specifications and automatically execute countermeasures during the on-going process, while ENGEL e-flomo compensates for temperature fluctuations in the mould and thus also contributes to high process consistency.
smart production for greater productivity
The smart production concept includes the entire machine park in its focus with the goal of increasing productivity. In the ENGEL e-factory, ENGEL has its own MES (Manufacturing Execution System) in its portfolio that is specifically tailored for the requirements of the plastics processing industry and thus achieves an extremely high level of vertical data integration all the way down to individual cavities. By supporting centralised access to all pertinent status and process data and comparing these with quality parameters, ENGEL e-factory improves transparency – both in local operations and at a global production network level. Thanks to the networking of all machines and locations, the processor can make optimal use of available capacities, query the status of all injection moulding machines at any time and create documentation very easily.
smart service: putting the focus on availability
The third core element of the smart factory is smart service. Remote maintenance and preventive maintenance are already a matter of course for many ENGEL customers and important components for high machine park availability. The new ENGEL e-connect customer portal has made the collaboration between plastics processors and ENGEL even easier and faster. For example, spare parts can be identified online and ordered immediately, and service requests can be sent via smartphone.
While the smart machine and smart production factors lie within the responsibility of the processor, some smart service solutions make it necessary for ENGEL as a supplier to have access to specific customer data as released by the customer for that purpose. "This requires more than mutual trust," emphasises Stefan Engleder. Defining security standards is one of the challenges that the fourth industrial revolution entails. "This is not just an internal issue for us, ENGEL is also actively involved at the Euromap level," says Engleder. "We are working towards a common information model on the basis of the OPC UA architecture. This technology-neutral concept offers a unique chance to achieve standardisation that we should definitely take advantage of."
From individual machines to a global production network
With inject 4.0, ENGEL helps its customers to achieve significant increases in productivity, quality and flexibility. The first three industrial revolutions also focused on boosting productivity, but each led to increased complexity as well. The fourth is also no exception here, but it is the first to directly include a solution for increasing complexity. Industry 4.0 provides manufacturers with the tools they need to master this complexity.
However, it is a different matter when it comes to flexibility. In the three previous industrial revolutions, production experienced substantial losses in terms of flexibility. Thanks to Industry 4.0, it is now again becoming possible – for the first time in 200 years – to boost flexibility up to or even beyond the level of purely manual craftsmanship. Industry 4.0 thus opens up the opportunity for the plastics processing industry to solve some of the major challenges of the future.
Industry 4.0 will be different for each injection moulding task, each company and each location – another fact that becomes clear in the inject 4.0 presentation at the ENGEL trade fair stand at Fakuma 2015. "There will be many future challenges and solutions that we cannot even imagine today," says Stefan Engleder. "The advantage of the evolutionary development of Industry 4.0 is the fact that each company can start implementing a specific solution adapted to its own requirements at any time and then gradually develop it further. Optimising manufacturing processes starts with the individual machines and can reach all the way up to a global production network."